Delineating between critical requirements and nice-to-haves can save cost and time. However, sometimes you have to go through missing requirements to learn. Here are a few stories and considerations to get you thinking as you scope your next project.
It’s not just designs. It’s about fit, form & function
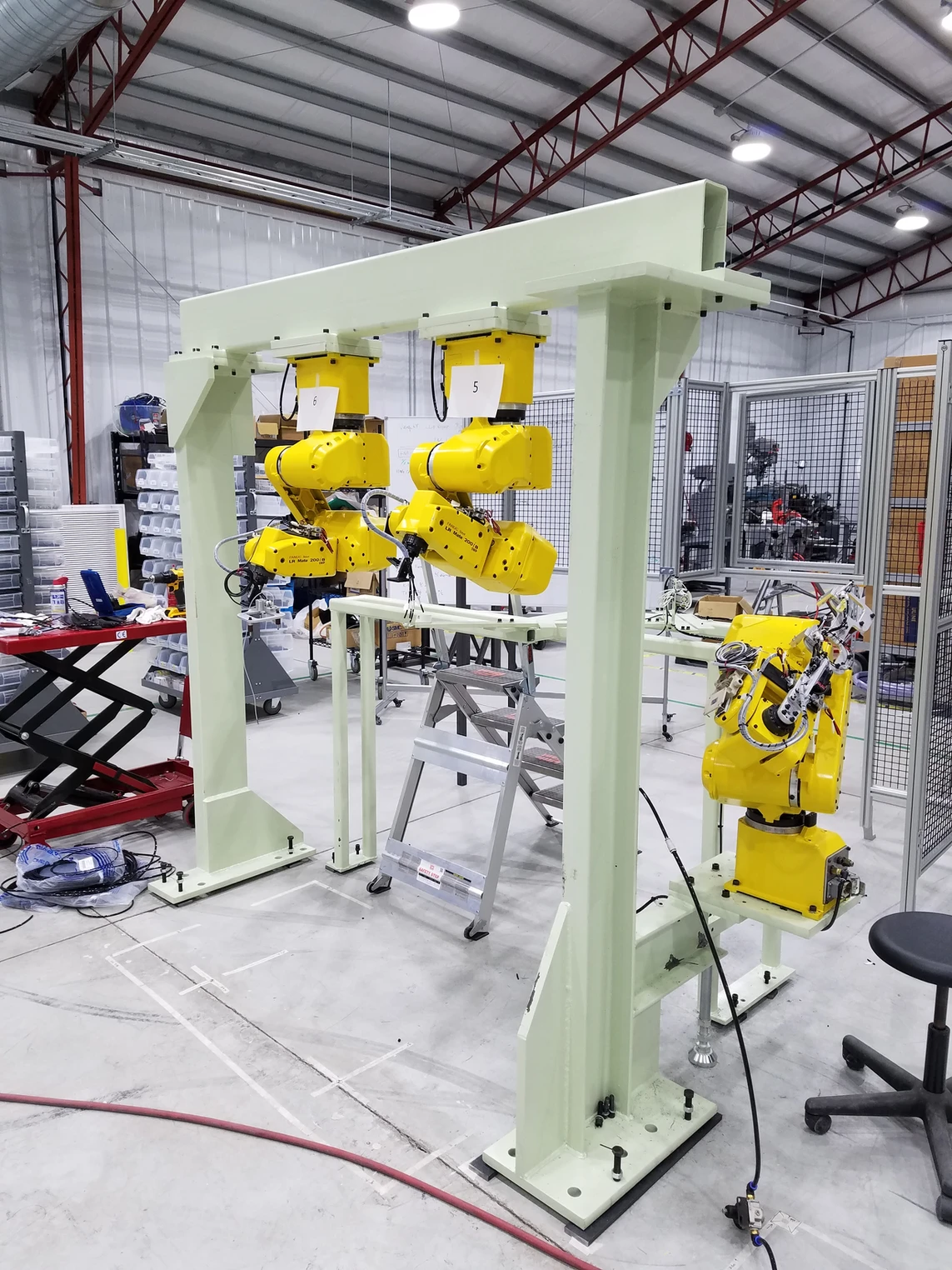
With one recent customer, we were asked to build a workstation in a small factory space where they were assembling parts for a large automaker in the US. The workstation would laser engrave serial numbers on aluminum castings. The designs that were given showed mirrored components.
When we got deeper into developing the design, the customer reached out because while the designs implied mirror requirements, they actually needed two left-handed components rather than left- and right-hand, mirrored components.
What features affect fit, form and function?
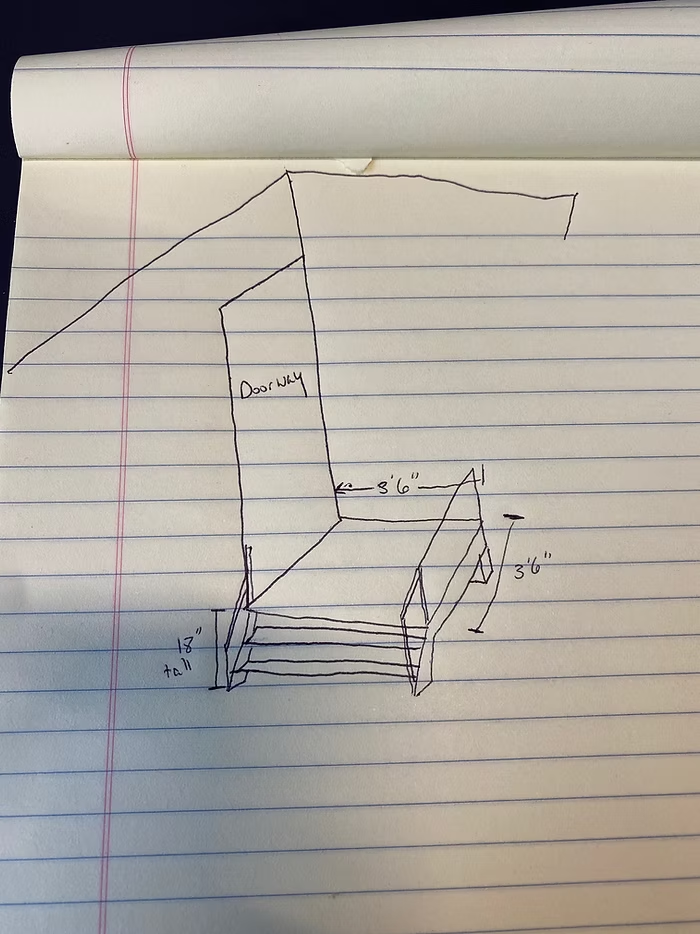
We always make every attempt to procure photos, videos or schedule an on-site visit to see how the piece is used in day-to-day interactions. Or, if a new application, it’s always helpful to receive any available information on operation/usage of components.
Drawings can be obsolete or when you get into the day-to-day application, more requirements may be needed. You can see that that having a drawing like the one shown here from a customer that we received won’t support the next iteration needed down the road.
Especially with parts that will be repeat orders or need improvements over time, converting hand drawn or obsolete drawings to 3D designs can reduce headaches the next time it comes up.
Are we building a doghouse for a hunting cabin or cabinetry for the Queen of England?
If all parts of the item do not need to be held to a high standard, then we have more options during manufacturing.
How critical are aesthetics?
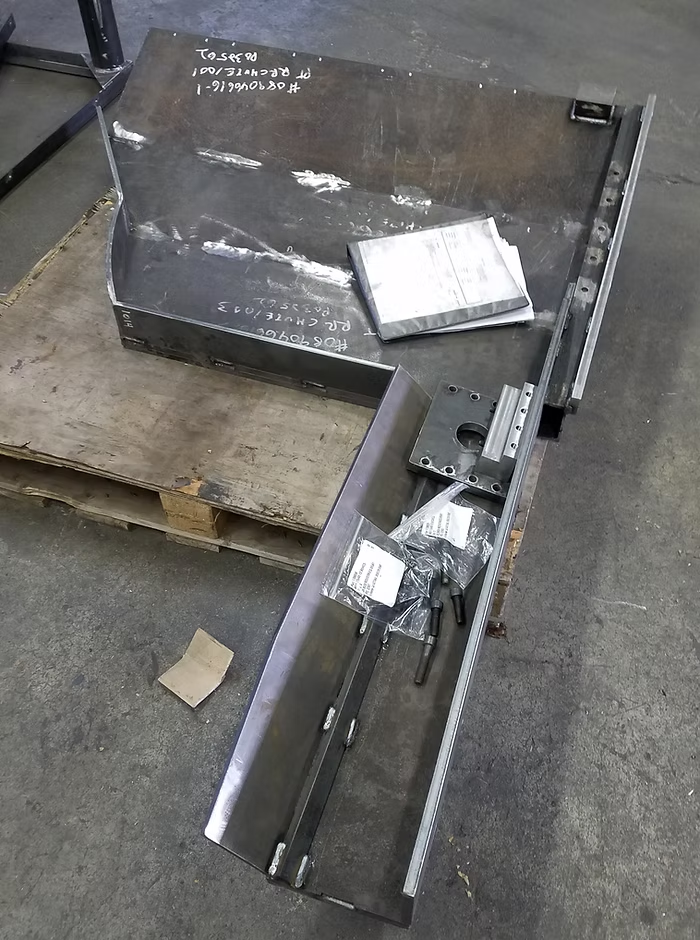
In this example, the customer requested tooling that would be supporting large, hot metals when exiting a forging process. Because of this, it required plasma cut pieces. That means that we would not need more expensive machining for smoother edge. The end piece did not require as tight of tolerance either.
However, the heavier material thickness was required because of the rough usage.
Read more about how we worked with International Crankshaft Inc. on a similar project.
With a second project that was requested, a customer required softer curves with horse stalls so that the horses wouldn’t be injured. This required a different bending process than originally scoped. Because of this request, there was additional cost.
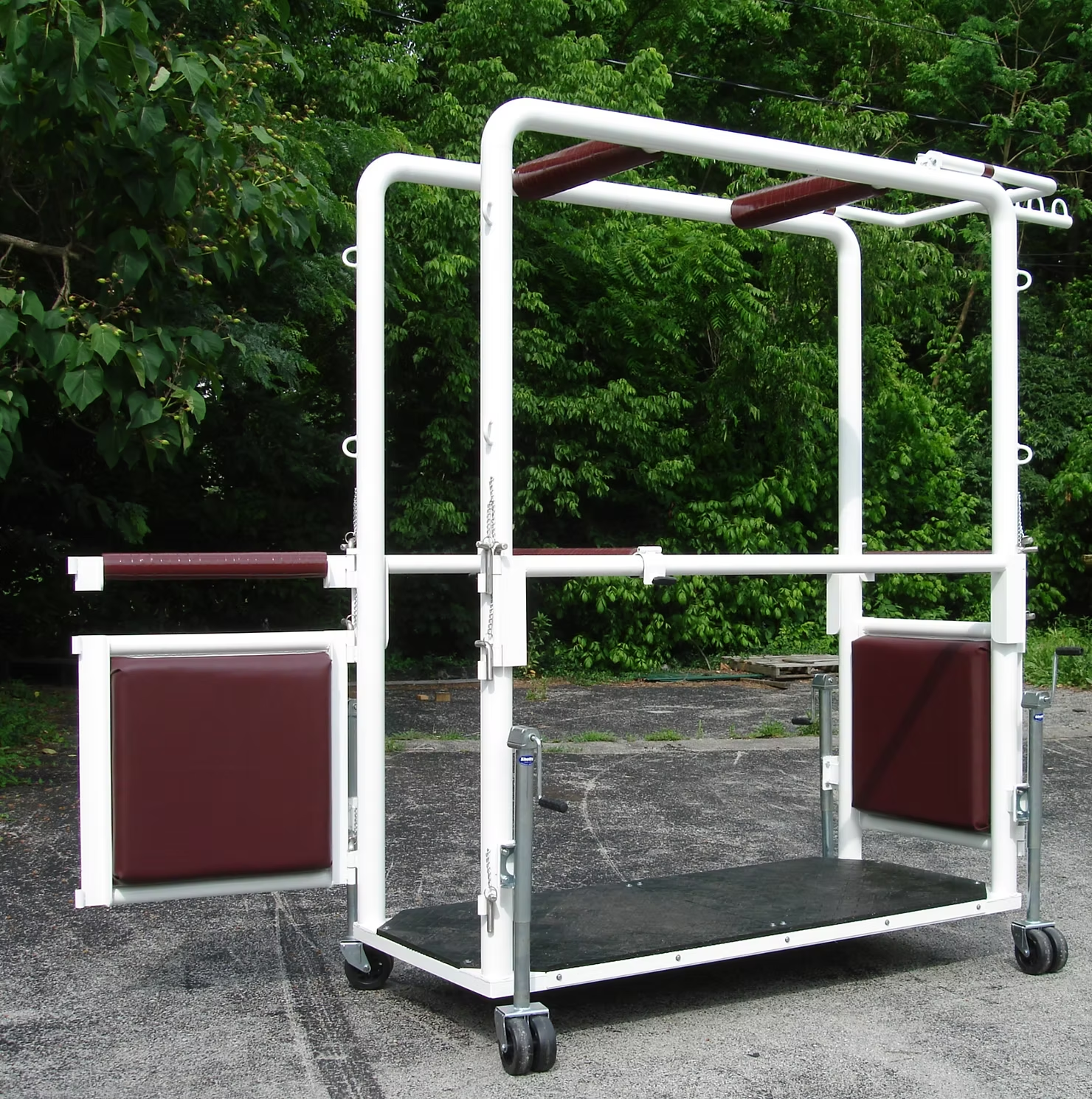
What features are critical?
When thinking about scoping your next project, it’s important to be clear about the nuances of touch surfaces & tolerances. It is often an afterthought but so important for the manufacturing process.
How does the surface need to differ based on where it is on the finished piece & how people interact with it?
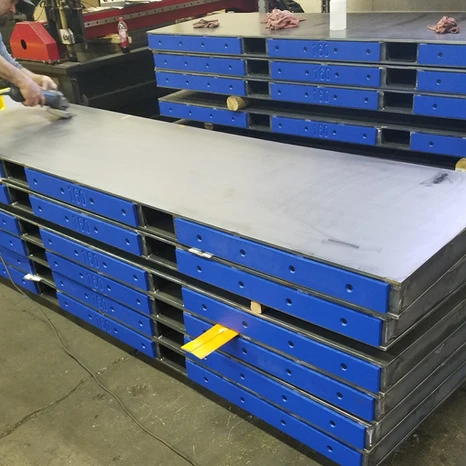
The touch surface in this example required hand grinding and acetone to remove any imperfections and oil on the top edge because it would be holding sheet metal blanks. However, the sides didn’t require any additional processing and could be rough, which saved on cost. Read the full case study.
Do you have a tolerance that will crash an astronaut or one that is flexible?
You may not need aerospace-like tolerance but appropriate tolerances still need to be on your radar. The type of tolerance that you require will determine the type of process that will be needed.
Does the part need to be machined, laser cut or plasma cut? Does the type of tolerance require a metal inert gas (MIG) or tungsten inert gas (TIG) welding?
-
MIG welding is often used when speed is required.
-
Even when performed well, MIG welds aren’t as clean as TIG welds, but the increased efficiency can be beneficial.
-
TIG welding uses a tungsten electrode to produce a weld. It allows for the greatest operational control and it creates stronger welds.
-
TIG welding is more complex and difficult to learn.
Close tolerance fitment an issue?
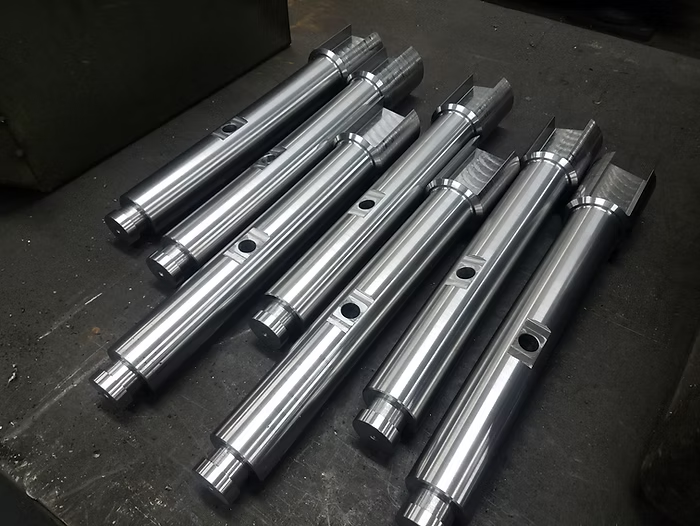
Then, we’ll look into whether we need to machine or laser. Rough weldment bracket? Then, we’d need to investigate saw or plasma, which may be less costly. The first example is a shaft that goes inside of crankshaft grippers.
There is a tight tolerance that rides inside of plane bearings. The bearings must be a tight fit so they properly locate the shafts. These pieces needed to be processed on both the ROMI D600 mill & ROMI C400 lathe to create the pockets, as well.
What tolerances are required and how exact do the placements need to be?
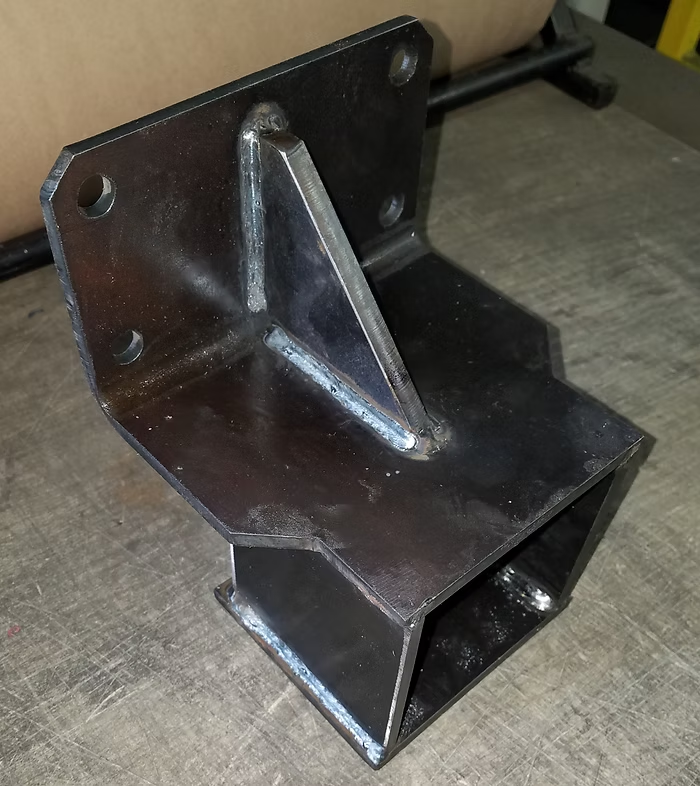
With this example, it didn’t require high tolerances. There are five holes and as long as they were generally placed properly. Bolts would be placed in the holes of the foot and would be holding large compressors and generators.
By defining the level of tolerance, you can avoid additional cost.